Petroleum Product of the Week: Baseballs
By
on Sep 23 2016
It's football season again, and for the second year in a row, I can happily admit that I do not give a crap.
The New York Mets are in the Wild Card hunt currently one game ahead and there is nothing in all of professional sports that takes precedence over a playoff berth for The Amazin's. Of course, this is just me.
Most people hate watching baseball. The games go on for hours, the action comes in spurts, and the risk for shocking injuries is likely the lowest in all of professional sports; and don't get them started on the infrequency of bench-clearing brawls.
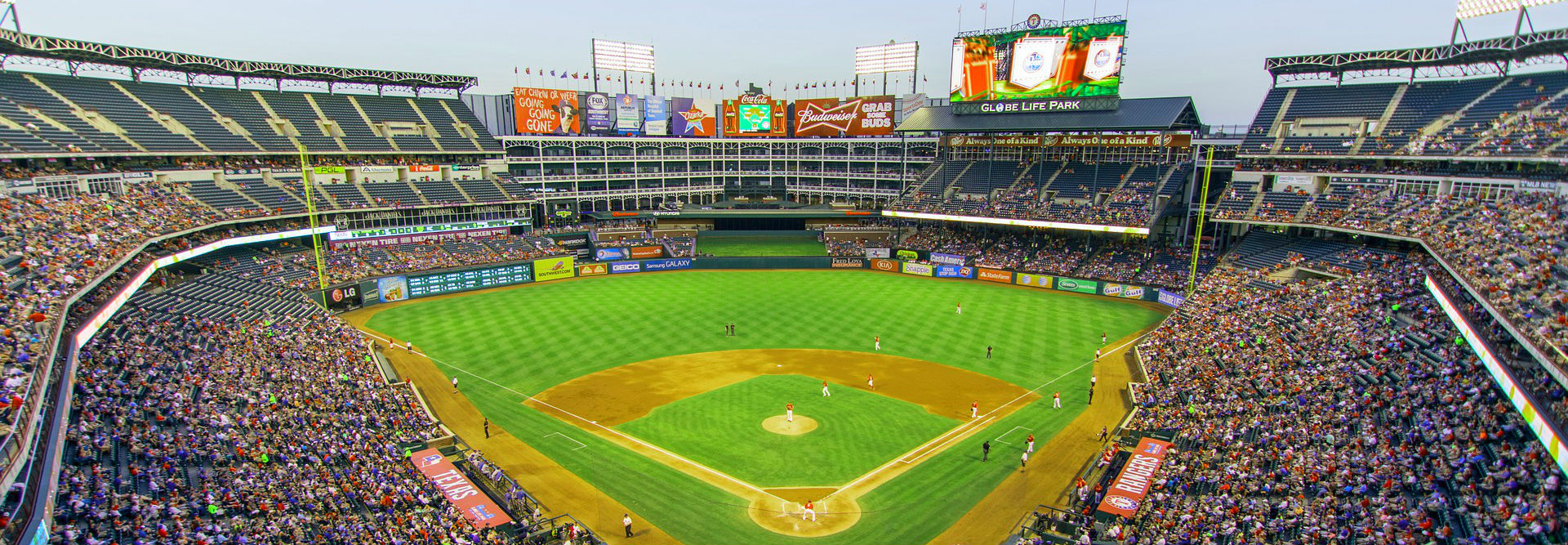
Baseball is a game for the patient. As a Mets fan, I've gotten quite used to waiting for something to happen. Yet, it's almost October once again, and the Mets actually have a shot so what more could I ask for?
America's pastime has undergone some drastic changes since the early beginnings of the game. In fact, I'm a part of the school of thinking that believes Babe Ruth (on his best day) would be the worst player in the league should he be transported into 2016 even more likely, he would have a lesser chance of getting a shot at the pros than Tim Tebow ...
..erm
.. .
Anyway, as the game has changed, so too has the ball itself. Initially, baseballs were made from the remainders of old shoes, tied messily together in a spherical shape these balls had four panels that were cross-stitched to make the seams. At the time, size and weight were subject to the discretion of the maker of individual baseballs, since most of them roughly sized up the objects as they worked.
Nowadays, baseballs are made in a manufacturing plant interestingly, Rawlings (the company that makes all of the MLB's baseballs) has a single plant in Costa Rica dedicated to making baseballs for the entire season. This is even more impressive when you find out that the average lifespan of a single baseball in an MLB game is seven pitches.
The petroleum-based components of a baseball are found at its very core: the pill, as it's commonly called. The pill is made from black, petroleum-derived rubber and a red rubber casing, with the center being made of pure cork. The combination of cork and rubber provide the springiness of a baseball, resulting in the towering home runs you might see from home run hitters such as Dozier and Encarnacion. Yet, petroleum's involvement doesn't stop there.
After the pill is wrapped in two different types of wool yarns, a third layer of yarn is added, made from a poly-wool blend. The polyester components of this yarn provide a smoother surface to the baseball's center, and makes the application of the cover more easily achieved. Two figure-8 shaped patches of leather are adhered to the center of the baseball. Next, a worker hand-stiches 108 knots into the baseball, the most time consuming process of baseball-making. Following this, the balls are pressed (most likely via a hydraulic system) and stamped with the MLB and Rawlings logos.
They may not have changed too much since the beginning of the game, but baseballs have certainly come a long way from the shoe shop.
Sources
http://mlbfancave.mlb.com/fancave/blog/article.js...