John Visits Clemco Industries: Day 1
By
on May 23 2016
Washington, Missouri: located fifty miles south of St.Louis, in The Heart of Wine Country, nestled on the western bank of the Missouri River.
I recently had the opportunity to visit this quaint little town that is home to nearly 14,000 individuals, most of whom have family roots stretching back nearly 5 generations since their German Ancestors settled the region in the late 1700's.
I was not here to shop in the downtown business district or to visit the many bars and restaurants located throughout the revitalized downtown (although I did partake at John G's Bier Deck and responsibly enjoyed an Augusta 1867 IPA with the owner and his dog, Hopps thanks for the tour, Terry.)
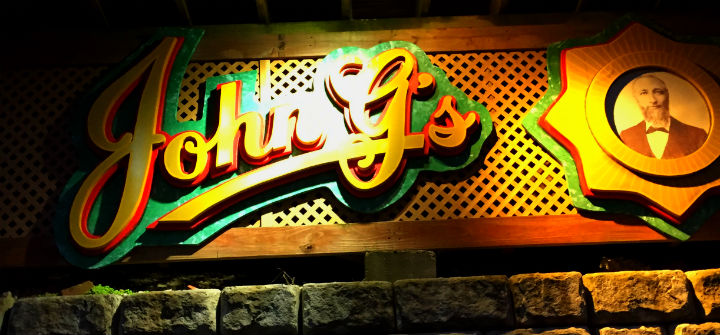
This trip was strictly business, and I was there to learn; representing Petroleum Service Company, I was offered the opportunity to participate in a 4-day training session at the headquarters of Clemco Industries, the leading blast machine manufacturer and partner of PSC.
Clemco Industries has called Washington home since 1991. Relocating from San Francisco fifty years prior, Clemco happened to be celebrating their 25 th Anniversary during my visit to Washington on April 14th 2016. Do the math and you can see that Clemco has been around for 75 years and that alone says a lot about a company. I was anxious to learn, be tested, and finally meet some of the great people and products that helped keep a company around for of a century.
Day One, Tuesday April 19th.
The day started at 7:30 AM with a meet and greet at Clemco Industries.
Upon entering the building you are immediately drawn to a bronzed blast pot just beyond the entrance way. The pot wears a plaque stating it is the first pot assembled in San Francisco back in 1941 pretty cool.

I made my way around the halls following the arrows to where we all will meet. I am greeted by a small group and immediately realized this class was going to be good. Large classes with a lot of participants are never really my thing and it is easy to get distracted.
This exclusive class held at Clemco Industries is limited to 14 participants and occurs twice a year.
Following a brief introduction, our group was treated to a tour of the manufacturing facility by LuAnne. It was incredible to see how rolled steel shows up at their shop and in a few weeks can be transformed into a fully functioning blast machine. Remarkably, the facility runs like a finely tuned machine the entire operation is a huge undertaking considering there are over 30,000 SKU's to keep track of.
We later came back into the class room to discuss corrosion, surface prep and surface profile taught by Hernan Azocar. Hernan not only discussed the different profiles but also how they are measured. We were taught how Digital Micrometers are used to measure different surface profiles. Pieces of steel with varying surface profiles were passed around so we could observe the differences in the profiles. While you'd think you'd strive for a smooth surface, you actually require your surface to be appropriately rough. Too rough of a surface may lead to increased corrosion while an insufficient surface profile (i.e. too smooth) will cause delamination or failure of a coating to adhere to a substrate.
Bottom line is: if you do not achieve the surface profile the coating manufacturer recommends, the coating will not adhere properly.
Side note: coatings and blasting go hand in hand rusted surfaces are often blasted first to remove any existing corrosion. Coatings are then sprayed, dipped, or painted over the freshly exposed metal to prevent rusting from occurring. If you've just recently blasted a surface, a coating might be a smart choice to finish and protect your job. You can learn more about coatings here.
We also discussed the different products Clemco Industries offers from Classic Blast Machines, Contractor Blast Machines, Zero Blast Cabinets, Aerolyte Systems for Non Aggressive Media, and Clemco Industrial Blast Facilities. This discussion laid a foundation for our week and what our agenda was going to look like.
It turned out that day one was focused on Blast Pots. Hands on Instruction was given on how to tear down and repair several components of the pot: the Flat Sand Valve FSV, the 1-1/2 " Piston Inlet Valve and the 1 " Piston Outlet Valve. 50+ year veteran Tom Geer and Aaron Wimmer, tech support, guided us through this process.
We then discussed how all of these parts work in conjunction with one another to form the TLR-300 Remote Control System. The day ended with a demonstration on the Pipe Painting and Pipe Blasting tools with some hands on experience on how to set up the carriages the tools are carried in.
Just like the well-oiled machinery housed in the manufacturing facility, Clemco's classes operated like clockwork. Needless to say, at the end of day one, the group and I were weary from traveling and a long day's work with lots of information. Still, not a single one of us wasn't looking forward to the next two days where we covered Blast Cabinets and standard safety.
These demonstrations served to help our group better understand the internal workings of Clemco Blast Pots and their ancillary components. Following the walkthrough, I can more confidently guide a customer through the process of rebuilding their valve and other blast pot components therefore, if you need any help with these machines, contact us at Sandblastingmachines.com and ask for John Gula: we're sure to be of some help.